Revved Carbon Technology is the bike industry’s newest and most advanced carbon fiber innovation. Covertly in development and testing for 3 years, Revved combines a revolutionary, patented manufacturing process and the next evolution carbon fiber material to create a new generation of mountain bikes. GG envisions a world where carbon fiber performance isn’t a badge of exclusivity but a welcome invitation to every one of you that wants to ride harder.
the benefits of riding revved

improved performance
- 300% more impact resistant than traditional carbon
- Reduces part to part variation
- Provides weight savings without sacrificing durability
- Lengthened product lifespan
- Improved ride quality thanks to its unique vibration damping properties

made in the u.s.a.
- Efficient manufacturing process
- Short supply chain
- A+ working conditions for our team

A more sustainable ride
- Economical to upcycle
- Ability to powder coat frames, eliminating VOCs (Volatile Organic Compounds) from the air vs wet paint
- Lengthened product lifespan = less waste
- Safe for handling
- Short supply chain dramatically reduces the carbon footprint (even the raw material is made in the US)Â
- 90% less sanding and finishing work minimizes air particulates
behind the scenes
Vital MTB sat down with the minds behind Revved Carbon to learn more about this revolutionary material. Chief Engineer, Matt, Director of Composites, Ben, and GG President, Will, sat down to discuss how Revved went from the drawing board to the trail.
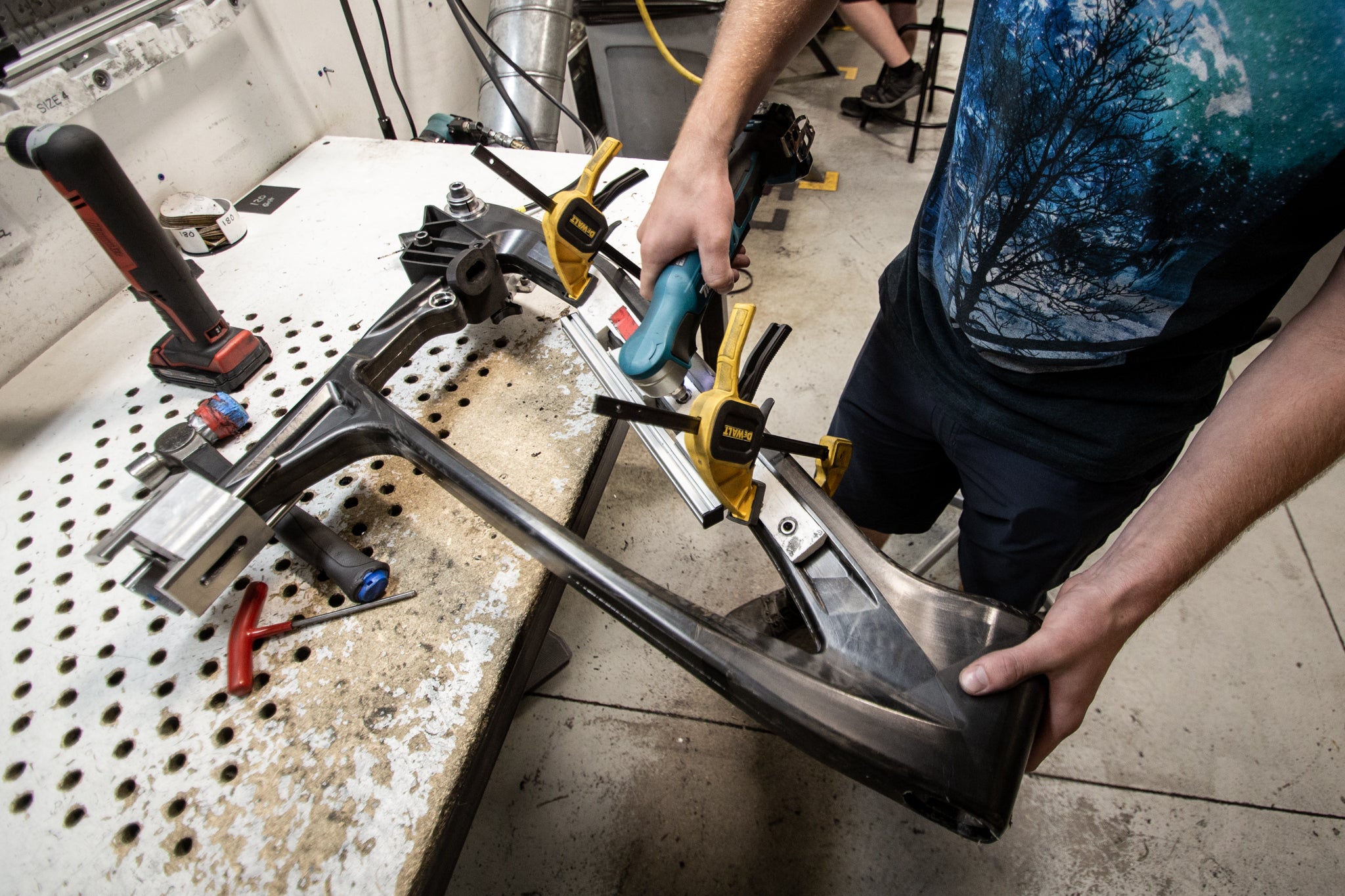
"The process ended up being so forward-thinking that Guerrilla Gravity won a $250,000 USD grant through the Advanced Industries Grant Program that's run by the Colorado Office of Economic Development and International Trade. Serious stuff, especially when it had only ever been awarded to companies in the aerospace, bioscience, and renewable energy industries up until now.
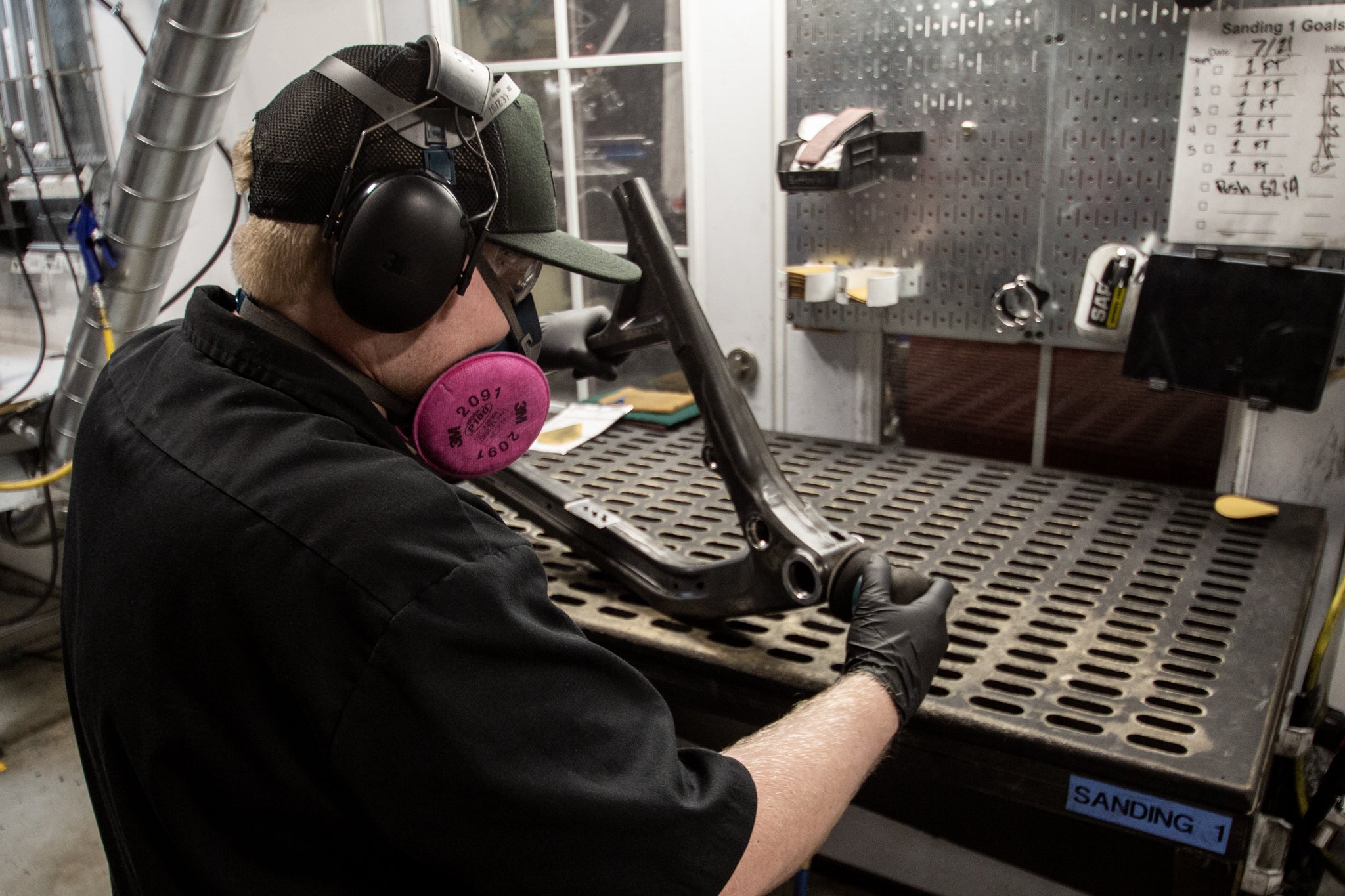
"Their move to American-made carbon frame is also a huge step in the right direction for the industry as a whole, and we applaud them for doing it right. The frames ride as good as they look, and have an unmatched attention to detail with a focus on easy maintenance and a rider centric design ethos.
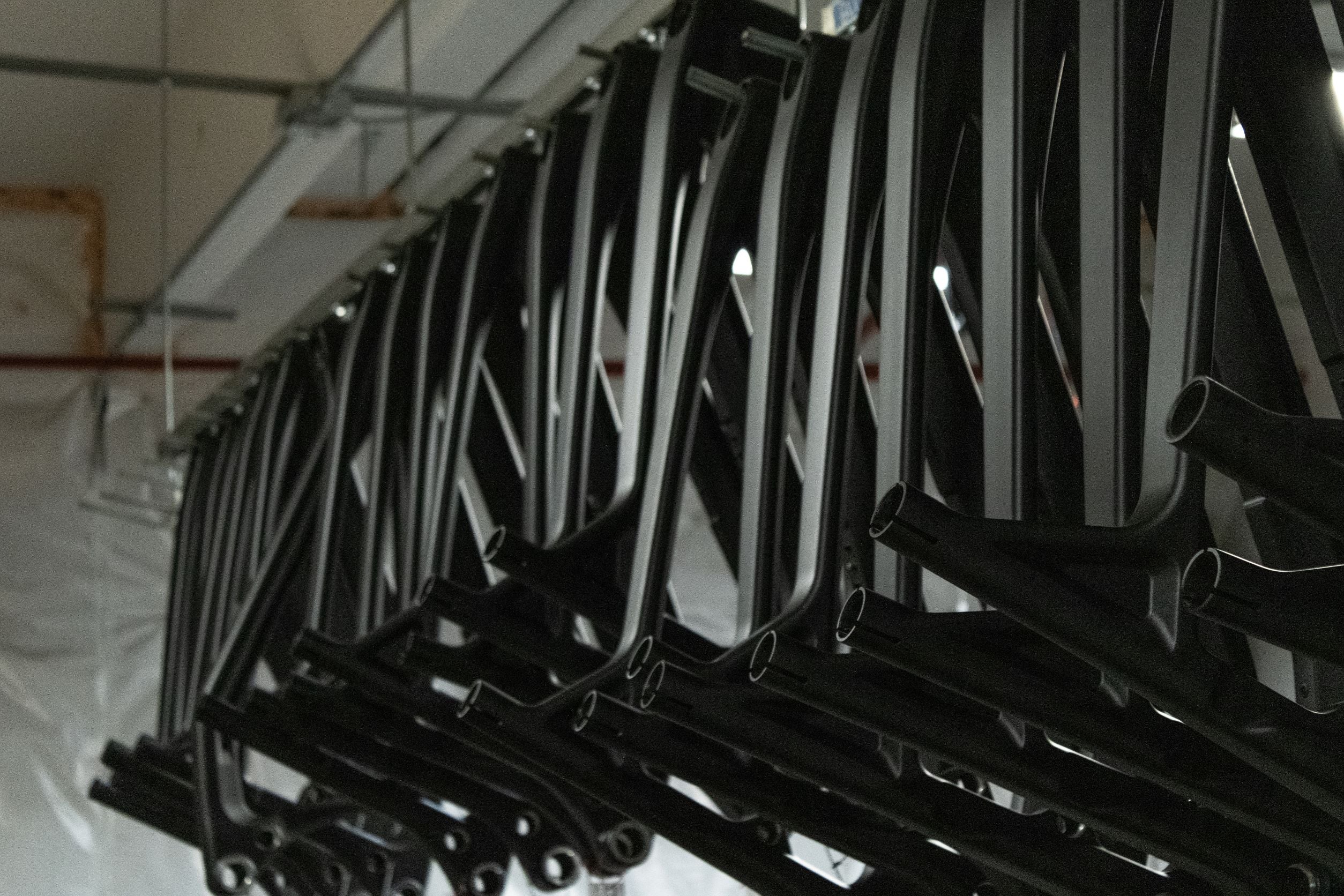
"Their new Revved Carbon Technology, which has been in development and testing for the last three years, combines an innovative, patent-pending manufacturing process to create the next generation of carbon fiber mountain bikes that are 300% more impact resistant.